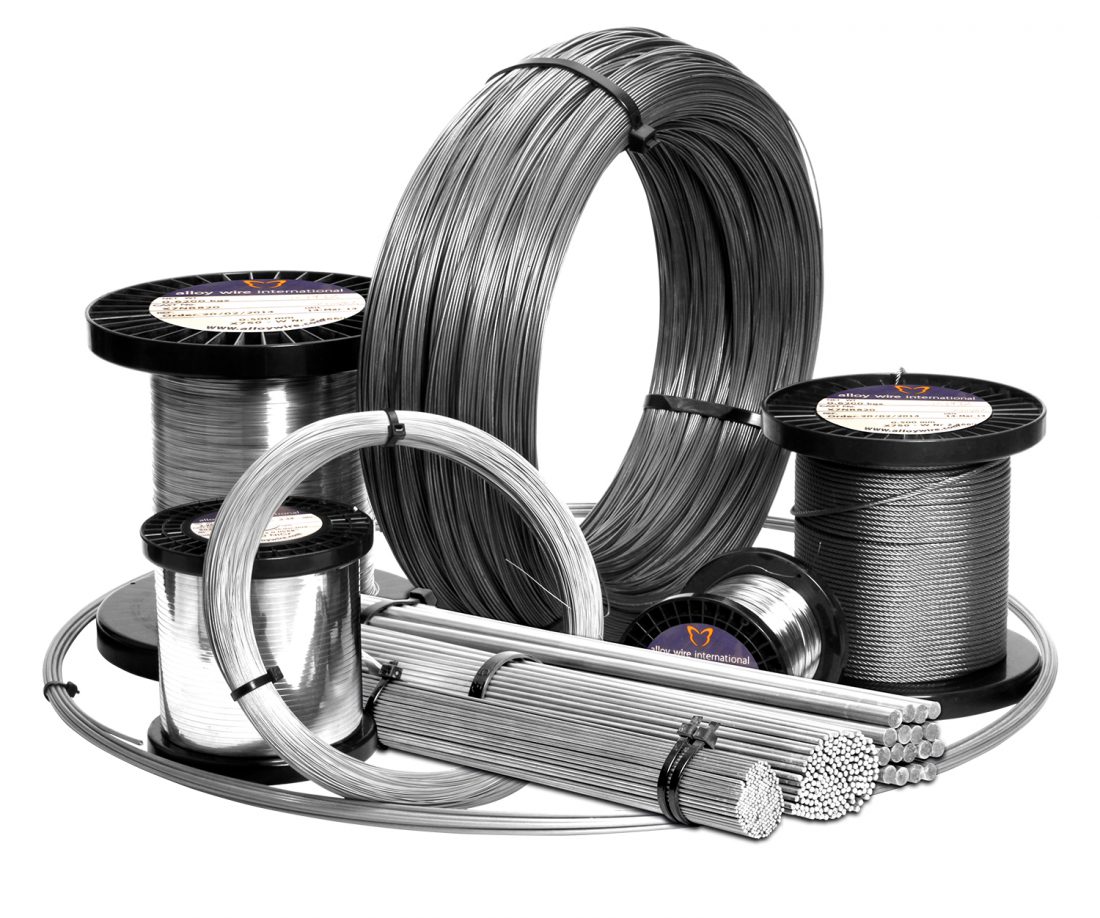
Phynox†
This Cobalt-Chromium-Nickel alloy gives a combination of high strength, ductility and good mechanical properties and is age hardenable. Phynox† also has excellent fatigue life, corrosion resistance in numerous environments and is non-magnetic. Phynox† often provides the ideal solution whenever high mechanical performance is required under severely corrosive service conditions. Its mechanical strength increases with cold rolling strain, while additional strengthening can be achieved by age hardening at 520°C. It is recommended to use Phynox† where a high resistance to corrosion and / or low relaxation at temperatures up to 380°C (715°F) are required. This alloy is used in medical devices, dental products, surgical implants and orthopedics. Phynox† is also known as Elgiloy, Conichrome and Alloy 3J21.